В настоящее время исследовательские и практические работы по совершенствованию существующих двигателей проводятся по следующим основным направлениям:
- улучшение системы зажигания,
- изменение процессов подачи топлива в цилиндры двигателей,
- установка дополнительных приборов,
- уменьшающих содержание вредных компонентов в отработавших газах.
Система зажигания оказывает существенное влияние на процессы сгорания топлива. Известно, что система искрового зажигания рабочей смеси с помощью традиционного распределителя-прерывателя не всегда удовлетворяет современным требованиям, связанным с полнотой сгорания топливу. Этот прибор достаточно «капризен». В условиях эксплуатации он не всегда надежно осуществляет зажигание смеси, а это сопровождается повышением в выхлопе продуктов неполного сгорания: окиси углерода и несгоревшего топлива.
Существенное улучшение в этом отношении дает применение бесконтактного электронного зажигания, которое обеспечивает более мощный разряд на свечах зажигания и отличается большей стабильностью работы. В последнее время система электронного зажигания получает все большее распространение. На некоторых новейших моделях зарубежных автомобилей эта система дополняется микро-ЭВМ, которая автоматически изменяет момент опережения, зажигания смеси в зависимости от нагрузки на двигатель и скорости движения, оптимизирует расход топлива и состав отработавших газов.
Для улучшения процесса сгорания топлива в цилиндре широкое применение находит так называемое форкамерное, или факельное, зажигание. Сущность форкамерного зажигания состоим в том, что в малой форкамере богатая смесь поджигается как обычно электрической искрой, а образующийся при этом мощный факел пламени зажигает основную часть более бедной рабочей смеси в цилиндре, что сопровождается улучшением сгорания топлива. Такие двигатели позволяют уменьшить выброс всех токсичных компонентов, включая и окислы азота, и при этом экономить до 10% топлива. Названная система применяется, в частности, на двигателях новой модели автомобиля «Волга-3102».
Изменение процессов подачи топлива в цилиндры достигается рядом приемов. Первый из них — это попытка установки на двигателе двух карбюраторов вместо одного. Выше отмечалось, что при работе двигателя на холостом ходу содержание в выхлопе ряда токсичных веществ увеличивается. Чтобы сократить количество этих веществ при работе двигателя на холостом режиме, нужно отрегулировать карбюратор на обедненную или бедную смесь (1 ч. бензина примерно на 20 ч. воздуха), но тогда двигатель не будет развивать необходимой мощности при работе с нагрузкой и не обеспечит надлежащей тяги и скорости. Выход из этого положения дает установка второго карбюратора, который регулируется на нормальную смесь (1 ч. топлива на 15 ч. воздуха) и питает двигатель на рабочих режимах.
Позднее были разработаны новые, более сложные конструкции карбюраторов, способных в одном блоке совмещать указанные функции и готовить необходимый состав рабочей смеси на любой режим работы двигателя.
Второй прием состоит в изменении клапанного механизма с целью более тонкого распыления и лучшего перемешивания смеси при поступлении ее в цилиндры. В ряде новых конструкций предусматривается регулирование высоты подъема впускных клапанов в зависимости от нагрузки, что улучшает процесс заполнения цилиндров смесью и сгорания ее.
Третий прием состоит в отказе от традиционного карбюратора и замене его приборами (форсунками) для непосредственного впрыска топлива во впускной трубопровод или в цилиндры. Эта система, впервые примененная в 1934 г.-на спортивных автомобилях, обеспечивает наилучшее распыление топлива и перемешивание его с воздухом, а также равномерное распределение смеси по отдельным цилиндрам. При этом способе не наблюдается оседания топлива в виде капель на стенках впускного трубопровода.
Система непосредственного впрыска особенно эффективна в сочетании с электронным управлением, которое автоматически дозирует топливо в зависимости от режима работы двигателя. Установлено не только снижение токсичности газов и экономия топлива, но и повышение мощности двигателей на 10—20%.
Некоторые устройства впрыска позволяют образовывать в зоне свечи обогащенную смесь (легко воспламеняемую от искры), а в остальной полости камеры сгорания — бедную. Такое послойное смесеобразование обеспечивает надежную работу двигателя при результирующей обедненной смеси. Указанное послойное разделение заряда получают различными конструкционными решениями, но чаше всего это направленный впрыск топлива в камеру сгорания. Система широко применяется на новых автомобилях за рубежом.
Разрабатываются и другие приемы для снижения токсичности отработавших газов на существующих типах двигателей. Однако многие разработки не полечили пока не только распространения, но и общего признания.
Отмечая положительные качества упомянутых выше конструкционных изменений, следует все же признать, что они не дают кардинального решения задачи. Кроме того, нужно иметь в виду, что подобные предложения можно осуществить на вновь выпускаемых автомобилях. Переделка же двигателей на действующих автомобилях практически не реальна. Поэтому важным направлением признается разработка различных типов нейтрализаторов токсичности отработавших газов, которые можно устанавливать не только на новых, но и на эксплуатируемых автомобилях с небольшими переделками.
Методы обезвреживания отработавших газов начали разрабатывать в СССР и за рубежом еще в 30-х годах, но практическое применение нейтрализаторы получили лишь 30 лет спустя.
Нейтрализатор — это небольшой прибор, предназначенный для снижения токсичности отработавших газов путем дожигания продуктов неполного сгорания (СО, СН, С) и разложения окислов азота на составные элементы — азот и кислород.
Первоначально полагали, что такие приборы будут просты в изготовлении, эксплуатации и дешевы. В Калифорнии (США) в 1959 г. был принят штатный закон, устанавливающий сроки оборудования всех действующих автомобилей этими приборами. Подобные предложения позднее были разработаны и в ряде других штатов США, а также в некоторых странах Европы. Однако реализация этих предложений оказалась не простой и существенно повысила стоимость автомобилей и расходы по эксплуатации.
Различают два типа нейтрализаторов: термические и каталитические.
В термореакторе, устанавливаемом за выпускным трубопроводом, осуществляется процесс пламенного дожигания окиси углерода СО и превращения ее в углекислый газ СО2, а также сжигание несгоревших в цилиндре углеводородов и альдегидов. Для интенсификации процесса дожигания в камеру термореактора подается дополнительный воздух. Реакция окисления проходит при температуре 500—600°С и снижает наличие углеводородов примерно в 2 раза, а окиси углерода — в 2—3 раза.
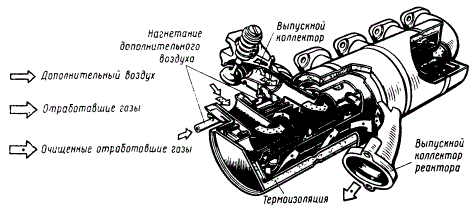
Термический реактор
На новых автомобилях термореакторы стали делать встроенными в выпускную систему двигателя с соответствующими изменениями в этой части конструкции двигателя. Каталитические нейтрализаторы, помимо окисления СО и СН, могут осуществлять еще и разложение окислов азота NOx.
В Советском Союзе в основном разрабатывается семейство каталитических нейтрализаторов. В Центральной научно-исследовательской лаборатории токсичности двигателей (ЦНИИЛТД) Министерства тракторного и сельскохозяйственного машиностроения СССР — одном из ведущих исследовательских учреждений страны в этой области спроектированы и испытаны нейтрализаторы марок Н-13 для автомобилей «Волга», ГАЗ-24 и Н-32 для автобусов ЛИАЗ-677. Расширенные испытания, проведенные на базе одного из московских таксопарков, показали, что разработанная система снижает уровень СО в отработавших газах на 80%, СН — на 70%, а NO — на 50%. В целом токсичность выхлопа уменьшается в 10 раз. Сконструированы подобные системы для грузовых автомобилей ЗИЛ и ГАЗ, а также для автопогрузчиков. Нейтрализаторы, разработанные в ЦНИИЛТД, позволяют достичь уровня токсичности отработавших газов, удовлетворяющего самым строгим требованиям. Процесс окисления СО и СН по существу беспламенный и протекает при прохождении отработавших газов через слой носителя (например, керамических гранул) катализатора.
Лучшим катализатором оказалась платина, но этот дорогой и дефицитный материал не может широко применяться. Предприняты поиски других, более дешевых и доступных катализаторов. Исследования показали, что в известной степени платину могут заменить палладий, радий, рутений, а также окись меди, окись хрома, окись никеля, двуокись марганца и др.
В нейтрализаторах советского производства используется окись алюминия.
Как и в термореакторе, процесс окисления СО и СН требует подачи дополнительного воздуха, а процесс восстановления окиси азота NOx не требует подачи воздуха. Современные каталитические нейтрализаторы выполняются в виде двухкамерного реактора. В одной из них осуществляется окисление СО и СН, а во второй — восстановление NOx.
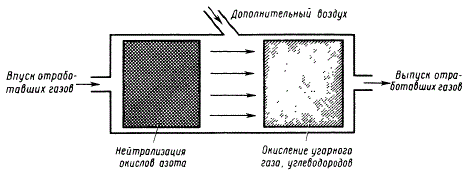
Схема двухкамерного каталитического нейтрализатора
Эти нейтрализаторы применяются на автомобилях с бензиновыми и дизельными двигателями. Одна из трудностей состоит в том, что в отработавших газах дизелей содержится 10% и более кислорода, в присутствии которого реакция восстановления окиси азота не происходит, а для окисления СО этого кислорода недостаточно. Поэтому обычные каталитические реакторы без дополнительных устройств обеспечивают у дизелей нейтрализацию несгоревших углеводородов и альдегидов, а также небольшую долю окиси углерода.
По мере эксплуатации созданных приборов обнаружились и другие неблагоприятные факторы. Так, при наличии бензинового двигателя с высокой степенью сжатия и поэтому работающего на этилированном бензине, поверхность катализатора быстро обволакивается свинцом. У дизелей на катализаторе осаждается сажа и сера, что существенно ослабляет действие катализатора и после определенного пробега он практически выходит из строя. Эффективность действия каталитического нейтрализатора существенно зависит от температуры в реакторе. Низкотемпературные реакторы работают при 100—300°С, а высокотемпературные — при 300—600°С и более. На первых моделях из-за высокой температуры корпус реактора достаточно быстро прогорал и требовал замены. Позднее этот дефект был устранен, для чего потребовалось усложнение и удорожание реактора.
Работы по созданию новых типов и конструкций нейтрализаторов продолжают во многих странах, но требования надежности и долговечности привели пока лишь к усложнению подобных приборов.
Одно из направлений состоит в снижении токсичности отработавших газов в результате их рециркуляции, т. е. повторного засасывания в цилиндры (вместе с порцией новой горючей смеси) с целью дожигания СО и СН и снижения количества окислов азота непосредственно в цилиндрах двигателя. Однако это ведет к некоторому ухудшению характеристик двигателя, не говоря уже об усложнении конструкции двигателя.
Источник: И.Я. Аксенов, В.И. Аксенов. Транспорт и охрана окружающей среды. Изд-во «Транспорт». Москва. 1986